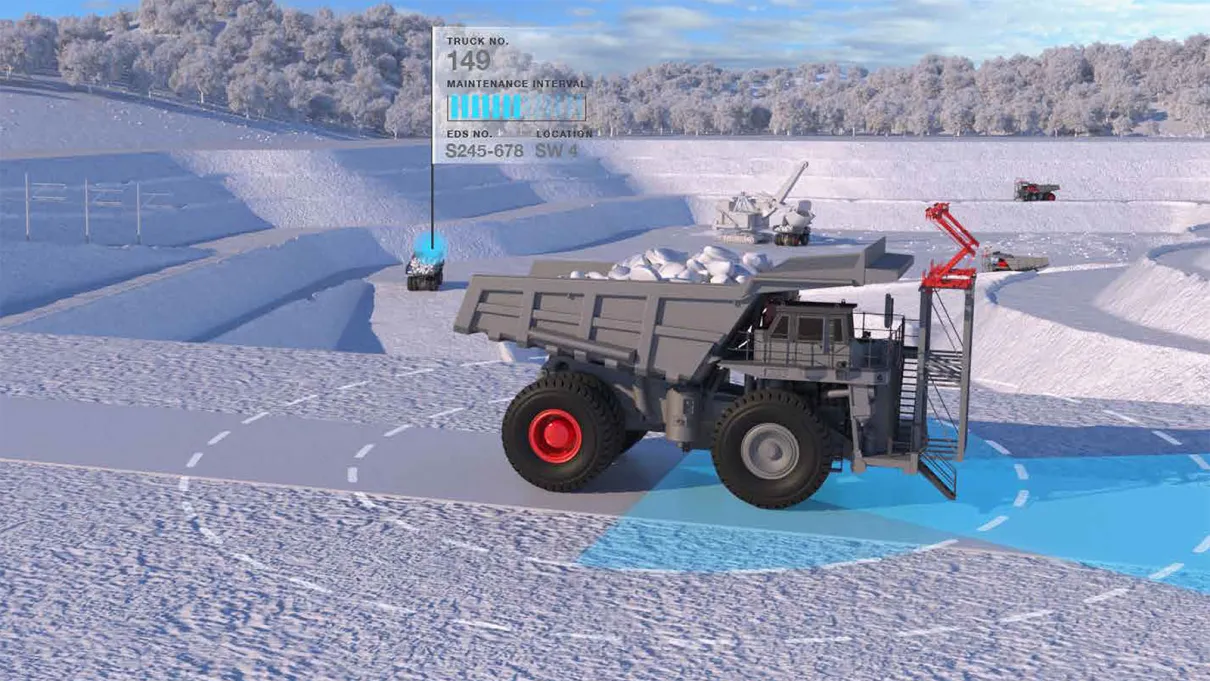
New Wabtec Collision Avoidance System Sets High Bar for Safety and Efficiency in the Mining Industry
Gen-3 CAS Features Predictive Curved-Beam Breakthrough and Contextual Alert Innovation
Playing with the “big” boys
While spot prices of metal and mineral commodities ebb and flow according to supply and demand, the combined market capitalization of the world’s top 50 mining companies remains massive, approaching $1.5 trillion in Q2 2024 (source: Mining.com).
Simply put, mining is “big” business in every sense of the word: its outputs power many economic segments and industries; it requires large-scale capital investment; and even the equipment it deploys is huge.
Consider a mid-size mining operation. Its fleet can typically consist of at least 250 pieces of heavy equipment, perhaps 60 of which would be haul trucks. And while the pick-up truck and “16-wheeler” drivers of the world may like to think they are operating “big rigs,” at 25-feet tall, with seven-foot high wheels, these mining haul trucks make the others look like toys.
And it doesn’t stop there. These haul trucks pale in comparison to other denizens of the mining operations. For example, excavators, at 35 feet in length and 30 feet in width, can pick up 80 tons of material in a single scoop.
A persistent point of failure
While the size of this equipment is appropriate for the scale of the job, it does contribute to making an active mining site among the world’s most dangerous work environments. Fortunately, ongoing innovation, increased oversight, and more deliberate planning have turned the tables on industry fatalities. Yet there remains room for improvement. Case in point, the Earth Moving Equipment Safety Round Table (EMESRT) attributes “30-40% of mining deaths each year to the failure of vehicle interaction controls.” (Emphasis ours.)
Understanding this number is way too high, the Wabtec Digital Mine team has doubled down on innovation across its mining solutions portfolio, unveiling a next-generation collision avoidance system (CAS) purpose-built to aid customers, and the mining industry as a whole, on their ‘zero harm’ journey.
A ‘safety first’ mindset
First things first. Wabtec’s safety record in mining is exemplary. Over the last 20 years, customers using Wabtec's CAS have experienced zero on-site fatalities.
While this strong performance record speaks volumes, Wabtec’s Digital Mine team knows every day on an active mining site comes with risk – that’s a constant. So the team keeps its focus on minimizing those risks, continuously improving the capabilities and usability of its solutions while integrating them tightly with the broader mission of the industry’s governing bodies, such as EMERST, and the safety and productivity goals of its customers.
“Every life lost in a mining operation is one too many,” says Mitch Tanzer, Global Commercial Director for Wabtec Digital Mine. “Technology can certainly help put our customers and their people in more control of their safety situation, but that technology needs to fit into a broader ‘safety first’ framework at their company. Technology alone is not the answer.”
Sensing a Step Change
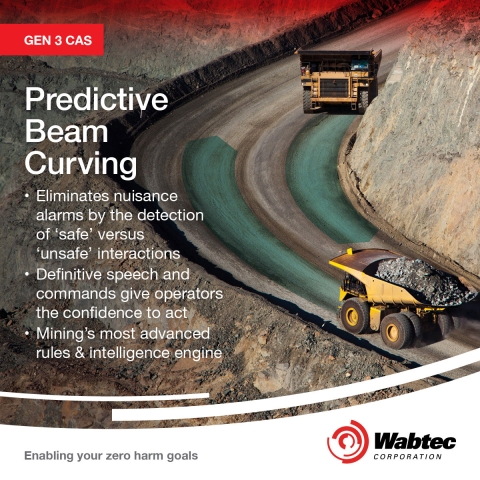
That said, the combination of strong EMESRT-recommended Level 1-7 safety controls (see Proximity Detection & Collision Avoidance Technology white paper, p.6) and the breakthrough capabilities Wabtec Digital Mine has reliably delivered the mining industry has made a measurable impact. And the new Gen-3 CAS from Wabtec only furthers this important work.
Armed with some of the most elite “sensing” technology in the industry, the Gen-3 CAS features high-precision GPS, which updates 50 times per second to deliver a relative location of each mining asset as it moves (or doesn’t) in real time. This extremely accurate broadcasting of relative position is crucial, because it enables vehicle operators (and the control centers that support them) to “see” other vehicles and assets in their path, and, in turn, to “be seen,” something that can’t be accomplished simply looking out the rearview or side-view mirror, or even out the front windshield for that matter, of a “house on wheels.”
This advanced sensing capability has been turned up a notch further by Wabtec with the invention, and introduction, of “predictive curved beam” technology. Imagine driving a humongous haul truck around a bend in a busy mine not knowing what’s coming in the other direction. The new technology factors in the vehicle’s dimensions and speed, the road’s width, predicts the path of the vehicle as it turns, and senses any oncoming traffic – and the physical attributes of that traffic – in a sub-second symphony combining physics, optics, and AI, which results in an appropriate alert as needed.
No cause for alarm
Another big step-change improvement in Wabtec’s Gen-3 CAS is in operator alerts. One of the biggest complaints from end users of collision avoidance systems is the frequency of false positives. When a system designed for safety beeps and buzzes every few seconds for seemingly no reason, the people it is meant to help become numb to it. Even worse, they begin to distrust it.
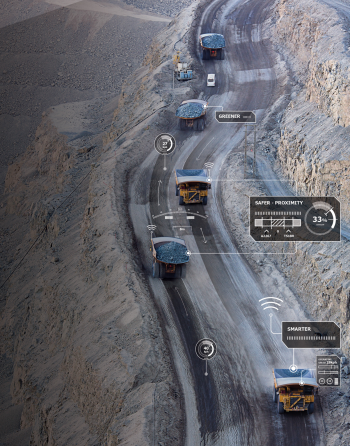
“Some safety systems are so ‘safe’ they seem to think everything is wrong,” commiserates Tanzer. “That’s dangerous, because if everything is wrong, nothing is wrong, and the system is rendered useless.”
Wabtec took this problem to heart and brought it all the way back to the drawing board. The Digital Mine team assembled mining operations leaders, vehicle operators, Wabtec designers and engineers, and an academic specializing in human-factors design to find a solution.
The result? New “contextual alerts” that do away with legacy “beeps and boops” (for the most part – studies find that a shrill alarm still works best as a last resort), replacing them with an escalating series of contextual voice prompts.
For example, a driver will want to know when he or she is tailgating (not only is visibility a problem in these big vehicles, so is getting them to stop quickly). And that’s not just to avoid a “fender bender”; accidentally smashing into the tray of a stopped hauler could cut an operator to pieces.
The new CAS’s sensing capabilities trigger a voice alert that tailgating is about to occur; then, if the driver doesn’t slow down, the next voice prompt will be more insistent: “Stop tailgating.” The other beauty of the system is that the driver in this scenario does not need to look at their computer screen to receive the alert.
A more involved scenario might involve a grader doing road work and a hauler looking to pass. The projected beam from the hauler will detect the grader asset, and the CAS will compute the proper passing distance, alerting the operator that there is road work ahead. The CAS will also provide this information on the cabin computer screen of the hauler.
Net net, good quality contextual information is provided to the operator right when they need it.
Like air traffic control, on the ground
While Wabtec’s Gen-3 CAS features many advances across its core hardware and software, its best capability may prove to be how it promotes safety while also enhancing operational efficiency.
Yes, the mining environment presents many risks, but it also poses tremendous opportunities. Every time a haul truck or other asset stops or gets shut down unnecessarily, the mine’s productivity drops. Just as air-traffic control keeps a vital fleet moving, so does an effective CAS.
“Safety is a journey, and our goal, and that of the entire mining industry, is ultimately reaching ‘zero harm,’” concludes Tanzer. “Our Gen-3 CAS represents the next big stage in this journey, one we hope will continue to keep people safe, while also making them more productive and their companies more profitable.”
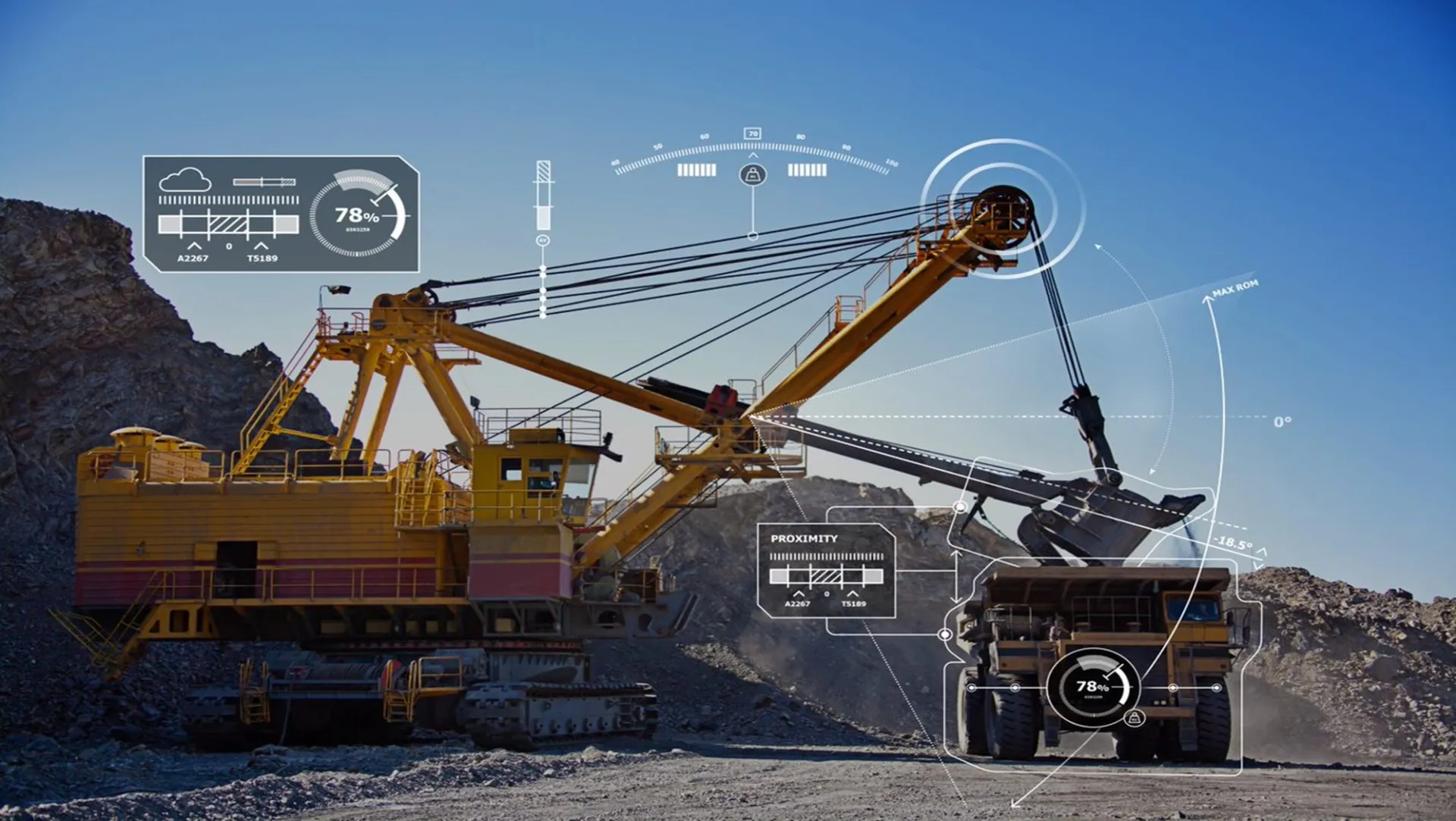