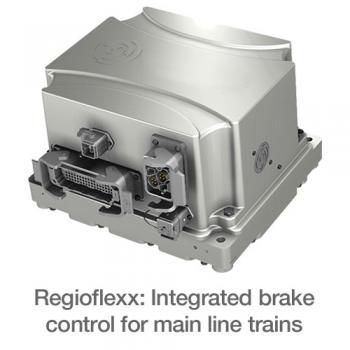
- Locomotive
-
Freight Car
- Freight Services
-
Digital Intelligence
-
Transit
RAIL COMPONENTS
Overview Braking Systems Couplers & Draft Gears Door & Access Solutions Electrical Solutions HVAC & Comfort Systems Power Collection Power & Auxiliary Energy Solutions Sanitation Systems Suspension & Vibration ControlBUS COMPONENTS
Overview Bus Components Doors & Accessibility E-Bus Charging Electric Power Collection Passenger Information & Vehicle SecurityDIGITAL INTELLIGENCE
Radar AIC Event Recorders iSmart Display Passenger Information & Video SecuritySERVICES
Transit Services - Mining
-
Adjacent Solutions
Adjacent Solutions
RAIL INFRASTRUCTURE
Overview Track Products & Materials Signal Wayside Components Vehicle Equipment Electric Power SupplyHEAT TRANSFER & ENERGY SOLUTIONS
Overview Diesel & Gas Engine Cooling Generator, Motor & Transformer Coolers High Temperature Applications